LA FIBRE DE CARBONE ET L'AUTOMOBILE
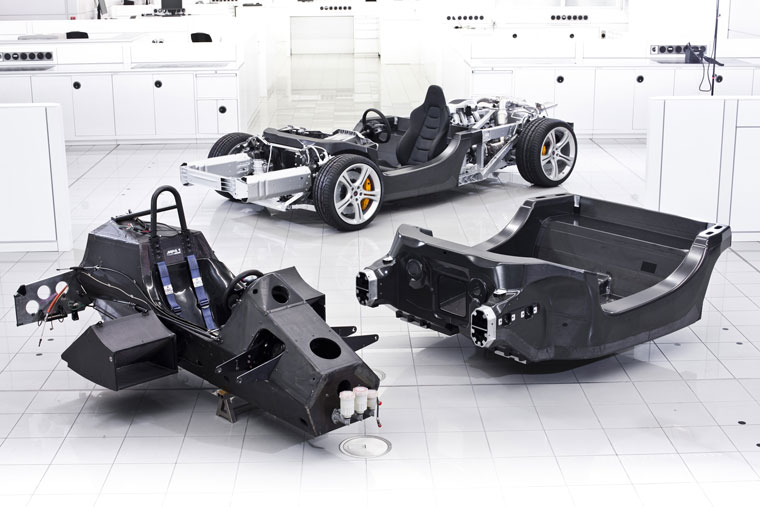
LA FIN DE L'ACIER ?
S'il est pointé du doigt sous sa forme dioxyde, l'emploi du carbone est de plus en plus fréquent et vertueux dans l’automobile. Un palier a même été franchi ces dernières années avec un arrivage « massif » de voitures disposant d’une cellule carbone ou de pièces composites à base de fibre de carbone. Deux solutions qui ne sont plus à présent réservées aux supercars hors de prix et qui vont tendre à se démocratiser dans les années à venir…
Texte : Maxime JOLY - Photos : D.R.
Pourquoi la fibre de carbone devient incontournable en automobile ? Parce qu'elle allie un poids maîtrisé à une rigidité maximale. Ce matériau est même considéré comme le plus robuste qu’on connaisse à l'heure actuelle avec un rapport résistance/poids sans équivalent. Ainsi, les structures en plastique renforcé de fibre de carbone sont jusqu’à 75% plus légères que celles en acier tout en se montrant 10 fois plus robustes. C’est ce qui fait que plusieurs constructeurs (principalement haut de gamme du fait de son coût de production élevé) ont suivi cette voie, notamment pour l'amélioration des performances et la réduction du poids...
LA FIBRE DE CARBONE, C'EST QUOI ?
Ce que nous appelons communément "fibre de carbone" ou même "carbone" concernant les pièces et structures automobiles est un abus de langage. En réalité, il faudrait parler de Polymère à Renfort Fibre de Carbone (PRFC), plus connu sous son abréviation anglaise CFRP (Carbone Fiber Reinforced Plastic) car dans son utilisation finale en automobile, il s'agit d'un matériau composite. Comme tout matériau composite, il se compose d'une matrice et d'un renfort. La matrice généralement utilisée dans la fabrication du composite CRFP est une résine époxyde (polyester, vinylester ou polyamide). Elle est renforcée de fines couches de fibre de carbone tissée dans un moule ayant la forme de la pièce définitive. Certains types de composites intègrent en plus d’autres fibres de renfort comme le Kevlar (voir encadré plus bas), l'aluminium, la fibre de verre, ou plus récemment le titane (carbotanium).
La fibre de carbone elle-même est plus ancienne qu'on ne le pense. Elle est née à la fin des années 50 mais son exploitation n'a réellement débuté que dans les années 70. Elle est constituée en majeure partie de graphite, forme cristaline stable et peu dense du carbone dont les propriétés mécaniques sont proches du diamant dans le sens parallèle au plan hexagonal, mais 30 fois inférieures dans le sens perpendiculaire. C'est pourquoi la fibre est ensuite tissée de façon croisée pour produire un matériau parfaitement résistant. La découverte du graphite est encore plus ancienne puisqu'elle remonte à la fin du 19e siècle ! Et nous la devons à Thomas Edison et Joseph Saw qui durant leurs recherches pour inventer un filament d'ampoule électrique firent carboniser du coton et du bambou, aboutissant au graphite.
Dans le cas de la fibre de carbone, on obtient également un matériau nouveau par modification physique d'un autre. On effectue d'abord une pyrolyse d'une base de polyacrylonitrile (PAN), un polymère de la famille des acryliques (photo à droite). Le processus comprend généralement l'oxydation des fibres de PAN pendant une à deux heures, à l'air et à une température voisine de 200°C. Puis, la carbonisation a lieu sous une atmosphère de diazote, à une température de 1 000 à 1 500 °C pendant seulement quelques minutes. Durant cette phase on élimine pratiquement toutes les molécules d'eau et d'acide cyanhydrique (HCN) et les atomes d'oxygène pour obtenir une structure graphitique orientée, un matériau composé à 90 % de carbone : la fibre de carbone.
Sa résistance varie entre le cinquième et la moitié de celle du diamant car il existe deux types de fibres de carbone. On parle de fibre de haute ou très haute résistance en traction, la deuxième étant obtenue après graphitation (phase supplémentaire nécessitant une température de 2 500 à 3 000 °C pendant environ une minute) pour obtenir un matériau composé à 99 % de carbone, beaucoup plus rigide (plus rigide que l'acier) mais aussi plus cassant du fait de son absence d'élasticité.
Dernièrement, les recherches se portent également sur les nanotubes de carbone, dont les propriétés sont encore bien supérieures à celles de la fibre de carbone. Une rigidité très élevée et une large déformabilité leur confèrent des propriétés d’absorption d’énergie surpassant celles des matériaux existants, tels le Kevlar et la soie d’araignée. Les nanotubes de carbone furent produits et observés dès les années 50 mais on commence à en explorer la mise en production depuis seulement une dizaine d'années. De telles fibres pourraient être incorporées dans des matériaux de protection ultraperformants et légers. Les nanotubes de carbone ont des propriétés qui suscitent beaucoup d'espoirs industriels, mais leur coût de production élevé et leur mise en application à grande échelle industrielle doit prendre aussi en compte les risques liés à la pollution nanométrique.
LE KEVLAR
Souvent associé à la fibre de carbone ("carbone-kevlar"), le poly(p-phénylènetéréphtalamide) ou PPD-T est un polymère thermoplastique appartenant à la famille des fibres d'aramides. Découvert en 1965 par des chercheurs de la société de chimie Dupont De Nemours, il est commercialisé depuis 1972 sous le nom déposé de Kevlar. Les premières applications furent pour des gilets pare-balles dès 1973. En effet, cette fibre synthétique possède de très bonnes propriétés mécaniques avec une résistance à la traction spécifique supérieure à celle de l'acier tout en étant beaucoup plus légère. Il n'est toutefois pas aussi performant que la fibre de carbone, pouvant atteindre une résistance à la traction de 7000 MPa, mais plus résistant à la rupture. Les deux matériaux sont souvent associés pour créer des pièces automobiles légères mais également de très haute résistance.
LE « CHASSIS CARBONE » EN VOIE DE DEMOCRATISATION ?
McLaren est pionnier dans l’utilisation de la fibre de carbone, que ce soit en compétition avec la MP4/1 dès 1981 (première monoplace dont le châssis est entièrement constitué de fibre de carbone) ou dans la construction de modèles de toute petite série au travers de la mythique F1. On tient avec McLaren le lien parfait entre la compétition et la voiture produite à but commercial. Le manufacturier anglais est toujours resté fidèle au numéro atomique 6, même lors de la collaboration avec Mercedes-AMG qui aboutit à la SLR. C’est donc tout naturellement que l’on retrouva l'utilisation du carbone lors du retour de McLaren Automotive avec sa propre sportive, en 2012. La MP4-12C ainsi que ses dérivés (12C, Spider, 650S et 675LT) sont basées sur la structure MonoCell (de 75 kg) en plastique renforcé de fibre de carbone dont la conception par les autrichiens de Carbo Tech s’est faite sous la supervision de Claudio Santoni de McLaren (à gauche sur la photo). La production du 5000ème châssis MonoCell a été fêtée en février dernier.
Chez Lamborghini, on expérimenta cette technologie dès 1982, avec un prototype de Countach à châssis carbone, mais son coût de mise en oeuvre face à un classique châssis tubulaire dissuada d'aller plus loin. Depuis le rachat par Audi, les financements ont cependant permis d'y revenir, notamment avec l'inauguration en 2010 d'un centre de recherche dédié, l'Advanced Composite Research Center (ACRC), doté d'un imposant four Autoclave (photo à droite). L'Aventador est le premier modèle de série de la marque à faire un emploi massif de fibre de carbone, notamment pour sa structure. Mais cela n'est pas l'apanage des grands noms, de petits spécialistes de la voiture de sport y ont également vu dans les années 90 un intérêt, identique à celui recherché en compétition. Les deux plus célèbres sont probablement Pagani et Koenigsegg qui n’ont cessé de faire évoluer leur cellule au fil des années. Si vous avez lu notre reportage exclusif sur la One:1, vous vous souvenez peut-être que le poids de la cellule a diminué de 20 kg par rapport à celle de l’Agera…
Ferrari introduisit sa première supercar à cellule carbone dès 1995, avec la F50, puis vint le tour de Porsche, bien plus tard, avec sa Carrera GT. Malheureusement, seule la KTM X-Bow avait rendue "accessible" (comprenez, sous la barre des 100.000 €) cette technologie. Deux constructeurs plus généralistes ont décidé de s'y investir à leur tour. C’est d’abord Alfa Romeo qui commercialisa la 4C à partir de 51.900 €, dont la cellule produite en Italie ne dépasse pas les 65 kg, mais aussi BMW, sur un terrain plus inattendu...
Pour compenser le surpoids lié aux batteries les constructeurs d'électriques n'ont pas d'autre choix que de construire léger tout autour, ultra léger même. C’est ce que BMW a mis en pratique avec son duo i3/i8. Bien que l’i8 soit inaccessible pour le commun des mortels, l’i3 demeure à l’heure actuelle l’offre la moins chère du marché. La moins puissante et la moins sportive aussi, mais c’est autre débat. En 2014, BMW Group et SGL Group ont signé un accord pour tripler la capacité de production de l’usine de production de fibres de carbone à Moses Lake (USA). Il s’agit d’un investissement supplémentaire de 200 millions de dollars. La capacité à moyen terme s’élèvera à 9.000 tonnes par an. Moses Lake deviendra alors l’usine de production de fibres de carbone la plus grande au monde.
Le principal inconvénient du CFRP reste son coût de production, actuellement de l'ordre d'un rapport de 1 à 10 au kilo de matière par rapport à l'acier. Cela étant, comme il faut beaucoup moins de carbone que d'acier pour obtenir une structure aussi rigide, le rapport final n'est plus aussi important. Il reste en défaveur du carbone, certes, mais l'écart tend à se réduire.
Souvent raillés, les américains et plus particulièrement Ford, se mettent eux aussi à la page. Ainsi la nouvelle Ford GT prévue pour 2017 a l’intention, l’été approchant, de suivre un régime allégé à base de carbone. Mais d’autres solutions requièrent la présence de matériaux composites…
LES AUTRES APPLICATIONS : LA CARROSSERIE CARBONE
Dans certains cas, les constructeurs automobiles vont moins loin dans l’utilisation de carbone mais l'objectif d'allègement reste la priorité. Son utilisation ne date d'ailleurs pas d'hier sur des voitures de production puisque les Ferrari 288 GTO et F40 disposaient d'éléments de carrosserie en carbone-Kevlar. Cela fut le cas plus récemment de l’Alfa 8C Competizione qui reste sur une base de Maserati GranTurismo mais bénéficie d’une carrosserie en carbone grâce au travail d’ATR Composites. 2008 marqua la sortie de l’Artega GT. Cette allemande conjuguait un poids de seulement 1.130 kg et un VR6 de 300 chevaux (le même que sur la Passat R36). Une recette imparable sur le papier mais qui ne prit malheureusement pas. A l’inverse, Joop Donkervoort, artisan néerlandais et ancien importateur de Lotus et Caterham, se porte bien. Certes, la D8 GT ne fut pas le succès escompté mais ce modèle a détenu le record sur le Nürburgring et obtenu un palmarès en compétition. Les clients sont plus friands de découvrables et c'est pourquoi la GTO lui fait suite avec sa carrosserie de roadster composée à 90% de carbone. Restons dans le monde des low-flyers avec les Zenos E10 et E10S qui profitent d’un châssis dit hybride et dont nous avons récemment appris l’importation en France. Pour l’occasion, un essai sera réalisé sur votre site préféré. Changement de décor avec l’Aston Martin Vanquish II qui profite elle aussi d’une carrosserie en carbone bien que cela ne se voit pas forcément sur la balance...
Terminons sur une note positive puisque la France n'est pas du tout en retard sur ces technologies. Le domaine aéronautique ayant permis très tôt à de petits spécialistes de se développer autour de la fibre de carbone (Carbone-Lorraine), nous avons au niveau national un vrai savoir-faire en la matière. Ainsi la carrosserie de la Tesla roadster, certaines pièces pour Aston Martin et McLaren Automotive, les ailes avant de l'Audi RS3 ou encore le capot avant de la Megane RS R26.R proviennent par exemple de chez Sora Composites, industriel français basé à Laval, en Mayenne !
RECYCLAGE
Longtemps pointée du doigt pour son problème de recyclage, la fibre de carbone trouve un nouveau débouché. Près de 10 % du polymère à renfort fibre de carbone (PRFC) mis en oeuvre sur la BMW i3 est issu de fibres recyclées, récupérées à partir des chutes de la production. Elles sont utilisées pour former le toit.
CONCLUSION
La fibre de carbone, ou "carbone" en faisant le raccourci, est indiscutablement un matériau à la mode car les ingénieurs cherchent par tous les moyens à réduire la consommation des voitures et la baisse de poids est une des meilleures pistes pour y arriver. Outre sa prolifération à l’intérieur des sportives, souvent à des fins esthétiques, le CFRP se heurte pour le moment à un double problème : un coût élevé et une production longue qui le prive de la très grande série dans le cas des cellules carbone. Reste aussi à mesurer l’impact du prix des réparations (actuellement une pièce carbone endommagée ne se répare pas...) et du recyclage, mais il ne fait aucun doute que de nombreux progrès sont encore possibles.